Protecting the Environment / Green Products
Green Products
Green Product Design and Management
WNC is dedicated to the development of communication technologies and green products. We define green products as those that meet the two major requirements of being safe and have low carbon emissions. In terms of safety, we require our products to be free from environmentally harmful substances, complying with regulations on prohibited and restricted substances management, ensuring they are harmless to human health and the environment. In terms of carbon reduction, we are committed to reducing carbon emissions throughout the five major stages of the product lifecycle: from raw material procurement, manufacturing, transportation, consumption, to waste disposal and recycling, thereby reducing our impact on climate change. Through adoption of environmentally-friendly materials and packaging materials use, optimizing low-carbon manufacturing processes, developing energy conservation technologies for products, and designing products for easy disassembly and recycling, we aim to reduce the negative environmental impact of products during each stage of their lifecycle, providing customers with energy efficient products and manufacturing services.
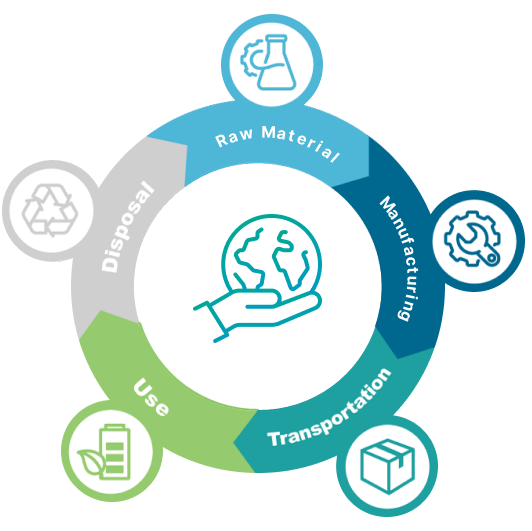
Raw Material
- Hazardous materials
- Designs that reduce material usage
- Environmentally-friendly materials: Recyclable, reusable, and low polluting materials
Manufacturing
- Introduction of the ISO 50001 management system, and establishment of energy saving goals
- Annual increase in the proportion of renewable energy use
- Optimize production processes and product yield to reduce waste and resource usage
Transportation
- Designs that reduce packaging volume to improve transportation efficiency
- Adopt low carbon means of transportation
Use
- Develop products with low energy consumption to reduce power usage when using the products
Disposal
- Introduce easily disassembled and recyclable product designs to improve material recycling rates
- Modular design increases the proportion of repairability to extend the product lifecycle.
- Build a product recycling system
Design for Green (DFG)
To achieve environmentally friendly product design, WNC adopts the PESTEL analysis approach, incorporating “meeting customer needs,” “complying with international regulations,” “reducing environmental impact,” and “promoting business growth” as key strategic directions. Through materiality surveys, WNC prioritizes relevant indicators to ensure that all factors relating to environmental impact and market demands are taken into account in the product design process.
We have established 50 checklist items as green design indicators in the following five categories: circular design, energy conservation, material usage, waste reduction, and green manufacturing. A data management platform monitors the compliance status of departments and products in regards to the aforementioned items. As of 2024, we have 82 product models that meet green product criteria. Through continued internal collaboration, we’ll work toward our goal of making our products 100% green.
Reducing the Environmental Impact of Products
R&D Innovation
WNC has adopted MuCell Microcellular Foam Injection Molding for manufacturing structural components of networking products starting from 2024. Experiments have shown that MuCell technology significantly reduces load on the driver unit, in turn reducing plastic usage by 10%. It also lowers energy consumption during material storage and heating processes, helping reduce overall carbon emissions by 5% to 10%. In addition, this technology greatly shortens the molding time, indirectly increasing overall production output by 10% to 15%.
WNC is also collaborating with the Hanoi University of Science and Technology in Vietnam to find more applications for MuCell technology in PC plastic molding so it can replace existing PC/ABS materials. Looking ahead, WNC plans to conduct further research on MuCell technology in Vietnam to offer customers diversified green design solutions and further its implementation of sustainable development practices.
Design for Energy Efficiency
WNC has always put emphasis on simplifying product design. In 2024, the company launched a home router equipped with a microcontroller unit (MCU), enabling the router’s power system to switch between different power modes as needed, significantly improving energy efficiency. Through an energy conservation simulation, we compared the power usage of the router’s four operating modes: normal mode, light sleep mode, sleep mode, and hibernate mode. Assuming that a router is in hibernate mode for eight hours a day, simulations showed that approximately 87.6 kWh of electricity can be saved annually per router. If we multiply that using the projected 2024 shipment volume, this translates to an annual carbon reduction of 504.13 tonnes CO2e.
Circular Design
To foster circular economies, we adopt the Cradle-to-Cradle (C2C) design framework, and recycling processes are taken into consideration during the initial phase of product design. This helps us extend product lifecycles and reduce waste generated.
In addition, we have incorporated the 5R design concept—Reduce, Reuse, Recycle, Redefine, and Redesign—in our product design process. During the design phase, we conduct simulations to find optimal hardware configurations, allowing precise product molds to be made, in turn reducing the amount of materials used and minimizing waste. For material selection, we use an internal material database to identify the recyclability and reusability of materials, ensuring that our products can be easily sorted and processed when they reach the end-of-life stage of their lifecycle. We have implemented easy-disassembly designs in our products, allowing specific components to be easily replaced during maintenance. This helps extend product lifespans and reduces the amount of waste generated due to product replacements.
Green BOM Database
In 2024, WNC, through internal data compilation and collaboration with value chain partners, established a database containing the carbon footprint information of raw materials used in products in the past two years as well as those of newly purchased materials. This Green BOM database is integrated with the material selection system used by R&D teams, allowing for product lifecycle carbon footprint assessments to be conducted during the product design phase. The database also facilitates the compilation of data for product carbon footprint certifications, significantly reducing the time and manpower needed for said work. In the future, WNC will continue to work with its value chain partners to reduce carbon emissions, promote the use of low-carbon materials and designs, and invest more in green product development.
Environmentally Friendly Materials
Post-consumer Recycled Resin
We propose the use of different recyclable/recycled materials to customers based on customers’ expected product specifications and the usability and durability requirements of communications products. To incorporate green product design concepts into product design processes of each unit more effectively, the Mechanical and Industrial Design Division initiated an Environmentally-friendly Attributes Database of Mechanical Components project in 2022. The database consolidates attributes of mechanical components that help reduce carbon emissions and waste, including the percentage of recycled materials used in these components so that R&D personnel can select the most appropriate materials during the design and material selection stage.
According to the product lifecycle assessment results, the use of product raw materials has had a significant impact on environmental indicators. Therefore, WNC collaborates with suppliers to develop recycled plastics, which are primarily used in product components and packaging. In 2024, products incorporating recyclable plastics accounted for about 12.24% of our total revenue for the year.
WNC’s Recycled Plastic Usage Note
Item | 2023 | 2024 |
---|---|---|
Total amount of plastics used (tonnes) | 3,376 | 4,413 |
Proportion of recycled plastics used to total plastics used | 8.82% | 16.88% |
Amount of carbon emissions reduced compared to if all plastics used were virgin plastics (tonnes CO2e) | 1,426 | 2,129 |
- Note: The data in this table represents plastic usage statistics for components manufactured in-house, and said data has been compiled and listed via units of weight since 2023.
Environmentally Friendly Packaging Materials
The packaging materials used to ship products, including corrugated cardboard, EPE, plastic bags, labels and stickers, manuals, pulp boxes, and blister shells, are all recyclable and environmentally friendly materials. Such materials comply with the restrictions on the four hazardous materials of lead (Pb), cadmium (Cd), mercury (Hg), and chromium (Cr6+) in the European Union’s Directive of Packaging and Packaging Waste (PPWD) 94/62/EC. In addition, WNC strives to reduce packaging volumes to improve space utilization, increase the amount of containers that can be loaded in a shipment, reduce the energy consumption and pollution produced during transportation, and reduce unnecessary transportation costs and carbon emissions. In addition, as a part of a sustainable forest initiative, WNC started using paper materials certified by the Forest Stewardship Council’s (FSC) Chain of Custody Standards (hereinafter referred to as FSC™ CoC) in 2014 and received FSC™ CoC certification in 2015. We regularly conduct internal audits and third-party verification to ensure that the packaging, corrugated paper bags, adhesive labels, and paper materials for printing that we use are made from trees grown in certified forests. As of the date of publication, all Taiwan and Vietnam sites have passed FSC™ CoC third-party audits.
WNC has introduced Cradle to Cradle (C2C) certified packaging materials, using non-toxic materials, clean energy, and water-saving processes to replace environmentally harmful materials and production processes that consume large amounts of energy. We have also established measures for recycling packaging. The reinforced craft paper tape for sealing product boxes and vegetable oil based inks for printing color boxes currently used by WNC are all C2C certified products. These products do not contain volatile organic solvents, both environmentally-friendly and good for employees’ safety and health.
WNC Product’s ESG Performance
Results of Carbon Emissions Reduction Measures
We have completed carbon footprint inventory for 12 products as of 2024. Based on the results of hotspot analysis, we have formulated carbon reduction action plans for each stage of the product lifecycle. To better manage emissions reduction, we categorize products into two groups: “Low carbon emissions” and “Emissions prevention.” We have taken the initiative in proposing sustainable product solutions to our customers and comparing the environmental impact of different materials and processes, enabling us to deepen our relationships with customers and work with them to develop green products that benefit us all. This approach not only reduces the carbon footprint across all stages of product lifecycles but also ensures compliance with relevant regulations and standards.
In 2024, we submitted an international green label application for one of our Wi-Fi extender products, and in 2025 this product will likely become the first WNC product to receive this certification. This represents not only a major milestone for WNC but also highlights our steadfast commitment to environmental responsibility.
Revenue Proportion from Green Products in 2024
Product type | Contribution to revenue | Definition (items meeting one of the following criteria are included) | Carbon reduction Note (tonnes CO2e) |
---|---|---|---|
Material manufacturing: low carbon emissions | 53.53% |
Use of low-carbon materials and packaging materials
|
2,129 |
Optimization of low-carbon processes
|
14,939.33 | ||
Consumer use: emissions prevention | 16.64% |
Energy-efficient design
|
1,528.24 |
Design for easy disassembly and easy recycling
|
n/a |
- Note: The amount of carbon emissions cut is estimated based on the variance in emissions between products improved by green design and their predecessors. Since products are used in different regions, the latest electricity carbon emission factors of current year from their respective regions are adopted for this calculation: 0.5568 kgCO2e/kWh for China sites and 0.3753 kgCO2e/kWh for U.S. sites.
Hazardous Materials Management Policy
WNC requires its suppliers to establish regulations concerning prohibited and restricted substances management. In addition, suppliers are also required to sign and follow the Supplier Statement on Non-Use of Environmentally Hazardous Substances to ensure that products and parts supplied (including bundled accessories, packaging, and other materials) to WNC comply with WNC’s prohibition of substances harmful to the environment and relevant international directives such as RoHS, WEEE, REACH, the European Battery Directive, and other related international standards.
For products shipped to Europe, the design complies with the EU WEEE Directive (2012/19/EU). During the development phase, principles such as recyclability and ease of disassembly are incorporated to enhance the efficiency of recycling and environmental friendliness at the end of the product lifecycle. Products also clearly display recycling symbols to facilitate appropriate recycling by consumers, demonstrating the company’s commitment to resource circulation and environmental protection.
Management of Prohibited and Restricted Substance
WNC has introduced lead-free production processes and enforced halogen-free standards in material specifications and production processes of products in order to reduce their environmental impact. WNC also utilizes XRF equipment in its plants to perform reliable and rigorous measurement and monitoring of prohibited and restricted substances in raw materials and products that are hazardous to the environment.
In addition, in order to enable procurement units and quality management related units to promptly and effectively confirm whether the raw materials provided by suppliers comply with customer specifications for prohibited and restricted substances, suppliers are required to upload their product composition analysis reports, inspection results, warranty cards, and related documents to WNC’s Green Product Management System. This helps us acquire the product material information from this management system and ascertain the performance of the green supply chain.
IECQ QC080000 Certification
Through the QC080000 hazardous materials management system, WNC ensures that products comply with regulations about restricted materials for electronic products listed by the European Union. IECQ QC080000 certification, which is developed according to the electronic component evaluation system of the International Electrotechnical Commission (IEC), is based on the ISO 9001, TL 9000, and IATF 16949 management systems. The certification incorporates a process-orientated method to reduce or eliminate hazardous substances in products and to further systemize hazardous substances management. It is capable of meeting RoHS, REACH, and special customer requirements.
Customer Health and Safety
WNC places great emphasis on user health and safety when designing products. We conduct safety tests on our products in accordance IEC 62368 and IEC 63000 standards for electronic product safety to ensure that the materials and components in our products do not pose energy, fire, or radiation related hazards under normal usage situations. In 2024, a total of 70 product models passed our safety tests. In addition, since consumers are usually most concerned about product performance and safety issues related to electromagnetic waves, all WNC products undergo Electromagnetic Compatibility (EMC) testing. This not only ensures the safety and stable performance of our products in all types of environments, but also prevents our products from interfering with other electronic devices.